PI Graphite 15%
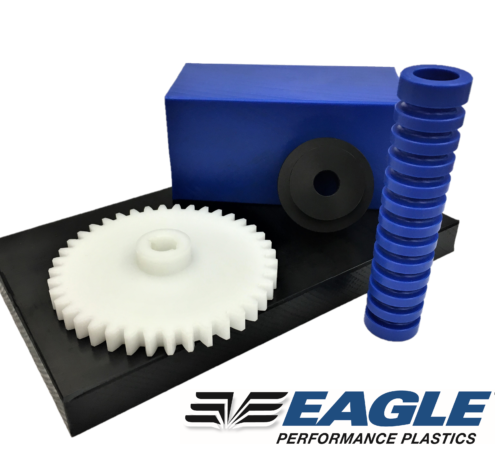
PI Graphite 15% Overview
What is the Material: PI 15% Graphite is an amorphous imidized material filled with 15% graphite.
Key Material Features: This material is beneficial in applications requiring improved friction and wear , while maintaining the properties of other PI materials including extreme temperature resistance, diverse chemical resistance, strength, and dimensional stability.
Other Considerations: This material is attacked by hot water/steam.
Physical
Property | Value | Typical ASTM Test |
---|---|---|
Chemical Designation | (PI) Polyimide | |
Trade Names (®, ™) | Tecasint 2021, Vespel SP-21, Duratron PI D7015G | |
Filler | 15% Graphite | |
Color | Black | |
Density (g/cm^3) | 1.46 | D 792 |
Mechanical
Property | Value | Typical ASTM Test |
---|---|---|
Modulus of Elasticity (Tensile Test) (psi) | 638000 | D 638 |
Tensile Strength at Yield (psi) | 14645 | D 638 |
Elongation at Break (%) | 3.0 | D 638 |
Flexural Strength (psi) | 20700 | D 790 |
Modulus of Elasticity (Flexural Test) (psi) | 587000 | D 790 |
Compression Strength: 10% Strain (psi) | 19300 | D 695 |
Compression Strength: 1% Strain (psi) | 4200 | D 695 |
Compression Modulus (psi) | 420000 | D 695 |
Impact Strength (Izod) (ft-lbs/in) | 0.80 | D 256 |
Hardness (R) | 126 | D 785 |
Hardness (D) | 87 | D 785 |
Hardness (M) | 73 | D 785 |
Coefficient of Friction (Kinetic, 40 psi, 50 fpm) | 0.25 | D 3702 |
Coefficient of Friction (Static) | 0.23 | D 3702 |
Wear (K) Factor (in^3-min/ft-lbs-hr) (Against Steel, 40 psi, 50 fpm) | 1.00E-9 | D 3702 |
Thermal
Property | Value | Typical ASTM Test |
---|---|---|
Glass Transistion Temperature (°F) | 660 | D 3418 |
Deflection Temperature (°F) (264 psi) | 600 | D 648 |
Service Temperature Continuous (°F) | 536 | |
Service Temperature Intermittent (°F) | 626 | |
Thermal Expansion (CLTE) (in/in/°F) | 2.30E-5 | D 696 |
Thermal Conductivity (BTU-in/hr-ft^2-°F) | 2.7 |
Electrical
Property | Value | Typical ASTM Test |
---|---|---|
Dielectric Strength (V/mil) | 186 | D 149 |
Dissipation Factor (1MHz) | 0.007 | D 150 |
Dielectric Constant (1MHz) | 5.42 | D 150 |
Other
Property | Value | Typical ASTM Test |
---|---|---|
Moisture Absorption (%) (24 Hours) | 0.44 | D 570 |
Flammability | V-0 |
The data stated are typical values intended for reference and comparison purposes only. The data should not be used as a basis for design specifications or quality control. The information is provided as a guide to the best of our knowledge and given without obligation or liability. Testing under individual application circumstances is recommended.